この記事には広告を含む場合があります。
記事内で紹介する商品を購入することで、当サイトに売り上げの一部が還元されることがあります。
半導体の前工程の検査プロセスといえば、最終的な電気的特性の検査を指す場合が多いですが、半導体プロセスの検査はそれだけではありません。
実は、各プロセス後にも様々な検査を行います。
半導体デバイスは微細な構造のため、製造過程での微小な欠陥や異物がデバイスの性能に大きな影響を与える可能性があります。
今回は、半導体製造の前工程における検査プロセスの紹介です。
目次 非表示
半導体の前工程では様々なモニタリングを行います。
前工程は、洗浄や成膜など化学的な要素が強く、結果を見ながら作業をすることができません。つまり、ウェーハを装置に投入すると検査をするまで処理の結果はわかりません。処理が終わってから後で調整するということはできないのです。
半導体の製造はある決まった値のものを作るという考え方ではなく、ウェーハ全体をある一定のばらつきの中に入れるという考え方をします。半導体プロセスはそのばらつきをいかに小さくし、各ロットの再現性をよくする必要があります。
したがって、装置の状態や各プロセスの結果を常にモニタリングしています。
前工程は大きく分類して、洗浄、イオン注入・熱処理、リソグラフィー、エッチング、成膜、平坦処理の6つのプロセスがあります。各プロセス後に行う検査は次の通りです。
- 洗浄
- パーティクル
- イオン注入・熱処理
- 抵抗値
- パーティクル
- リソグラフィー
- 重ね合わせ
- 寸法
- パターン欠損
- エッチング
- 形状
- パターン欠損
- パーティクル
- 成膜
- 膜厚
- 抵抗値
- パーティクル
- 平坦化
- 膜厚
- パターン欠損
- パーティクル
- ウェーハ検査
表面検査装置
表面検査装置は、ウェーハ表面のパーティクルを測定する装置です。主に加工をしていないベアウェーハや膜付きウェーハといった表面にパターンのないウェーハの検査ができます。
ウェーハ上のパーティクルは歩留まりの原因になります。ウェーハの表面にパーティクルがあると配線形成の際にパターンが断線したり、形状不良を起こしたりします。したがって、各プロセス後や装置内のパーティクルをモニタリングする必要があります。
パーティクルの検出の原理は、光学散乱式が用いられます。Arイオンレーザををウェーハ表面に照射して、パーティクルにより散乱された分を検出器で検出して、パーティクルの大きさ、個数、位置などを検出します。分解能は0.08μmまで可能です。
パターン付きウェーハ欠陥検査装置
パターン付きウェーハ欠陥検査装置は、配線の加工がされたウェーハのパーティクルや欠陥を検査する装置です。パターン付きウェーハの表面のパーティクルや欠陥を検出するのは、ベアウェーハや膜付きウェーハよりも難しくなります。
パターン付きウェーハ検査の原理は、明視野画像のパターン比較法が主流です。これは照明光をウェーハに照射して、カメラでウェーハの表面を撮影して画像としてパソコンに取り込み、正常なパターンの画像と取り込んだパターンの画像を比較することで欠陥の検出を行うものです。同一パターンを比較することで下地のパターンや凹凸形状の影響を排除して、欠陥を検出することができます。
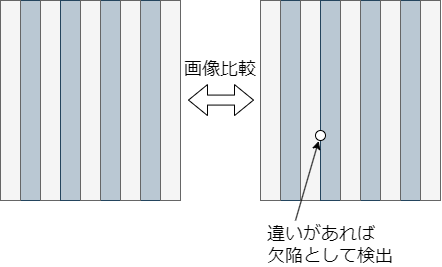
SEM
SEMとは、Scanning Electron Microscopeの略で走査型電子顕微鏡のことです。
電子線を絞って電子ビームとしてウェーハの表面に照射し、生じる二次電子や反射電子を検出することで高分解能で対象を観察する事ができます。さらにオプションで元素分析機能を追加することで、観察対象の成分を分析して不良解析などにつなげることができます。
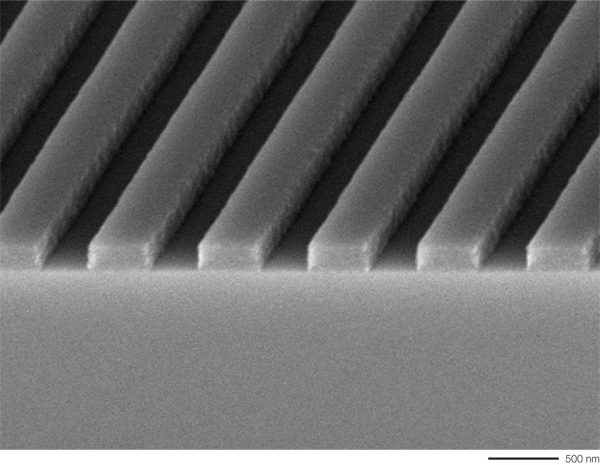
測長SEM
上記のSEMはウェーハの表面を観察することが目的でしたが、測長SEM(CD-SEM:Critical Dimension-Scanning Electron Microscope)は現像後のフォトレジストパターンの寸法計測やエッチング後の配線幅などの寸法計測を目的とします。
計測の原理は、SEM画像の濃淡(コントラスト)信号を用います。コントラストのラインプロファイルから指定した箇所の寸法を求めます。
重ね合わせ検査装置
半導体のプロセスは何十枚ものマスクを用いてパターンを重ねてゆきます。重ね合わせ検査装置は、リソグラフィープロセスで転写されたパターンの重ね合わせ精度を求め、誤差を計測します。
重ね合わせ検査の原理は、ウェーハにあらかじめ形成されたマークとレチクル上のマークの重なりのズレを検出します。マーク自体の大きさは20μm程度です。このマークやレチクルは各ショットの四隅に設けられています。1枚のウェーハ内で数ショット分を測定し、データは統計的に処理されて露光装置にフィードバックされて位置の調整に用います。
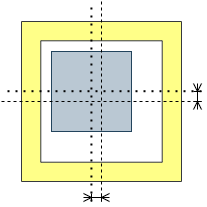
膜厚測定装置
膜厚測定装置は、成膜工程で加工した膜厚の測定を行います。
膜厚測定法としては、一般的に分光式を用います。分光式では屈折と呼ばれる現象を利用します。膜に光を当てると、屈折率の違いで膜の表面で反射する光と、膜の内部で屈折して基板表面で反射する光に分かれます。この光を検知して、あらかじめわかっている膜種の屈折率から計算して膜厚を測定します。
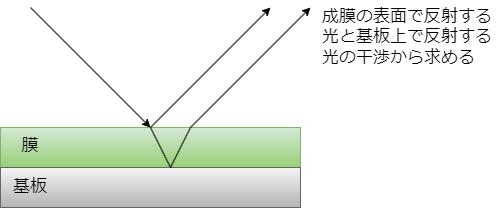
ウェーハ検査装置
前工程で作製したウェーハ上には、たくさんのチップが形成されています。前工程の最終工程は、各チップの電気的な特性が良品か不良品かを判断するテストを行います。
ウェーハ検査装置は、チップの電気的な特性を検査するテスタ部と、ウェーハの搬送及びプローブ(検査用の針)の位置決めを行うプローバ部に分かれています。テスタとプローバは別々のメーカーが担当し、それを組み合わせてウェーハ検査装置になります。
検査の手順は、プローバにセットした複数のウェーハを一枚ずつ取り出します。各チップのパッドと呼ばれるプローブの針を立てるところに針を当てて、入力に対して正しい出力が得られるかを測定します。
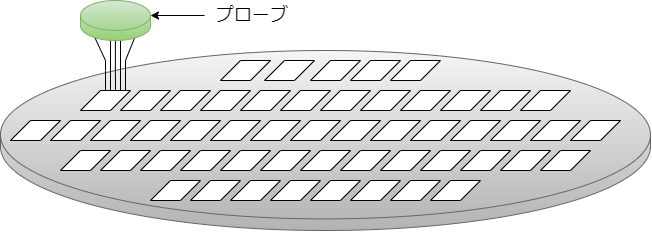
表面検査装置
- 日立ハイテク(日本)
- KLA(米国)
パターン付きウェーハ欠陥検査装置
- SCREEN(日本)
- 東レエンジニアリング(日本)
- KLA(米国)
- Onto Innovation(米国)
SEM・測長SEM
- 日立ハイテク(日本)
- アドバンテスト(日本)
重ね合わせ検査装置
- 東レエンジニアリング(日本)
- KLA(米国)
- Onto Innovation(米国)
膜厚測定装置
- SCREEN(日本)
- KLA(米国)
テスタ
- アドバンテスト(日本)
- Keysight Technologies(米国)
プローバ
- 東京エレクトロン(日本)
- 東京精密(日本)
以上のように、半導体の検査プロセスは多岐にわたります。
これらの検査プロセスを通じて、半導体デバイスの品質と信頼性が保証されます。
- 佐藤淳一「図解入門よくわかる最新半導体製造装置の基本と仕組み」、秀和システム (2019/12/10)
- 株式会社日立ハイテク