この記事には広告を含む場合があります。
記事内で紹介する商品を購入することで、当サイトに売り上げの一部が還元されることがあります。
半導体の製造プロセスにおいて、洗浄は極めて重要な工程の一つです。
微細化が進む半導体デバイスでは、微小な粒子や不純物が歩留まりや製品の品質に大きな影響を及ぼします。
洗浄プロセスは、半導体製造工程の約3割を占めています。製造工程のさまざまな段階で行われ、不純物や残留物を取り除き、ウェーハの表面を清浄に保つことが目的です。
なお、洗浄後は必ず乾燥させて洗浄装置から外に出します。洗浄と乾燥はワンセットになっており、これをドライイン・ドライアウトと言います。
今回は、微細な不純物や汚れを取り除く洗浄プロセスの紹介です。
洗浄プロセスで除去の対象となる主な汚染物質・付着物は以下のものです。
汚染のことをコンタミネーション(コンタミ)と呼んだりします。
パーティクル
パーティクルと呼ばれる空気中に浮遊するゴミや塵埃がウェーハに付着します。サイズは最大で数μ m、最小では0.1 μ m 以下となります。
半導体の製造には、空気中の浮遊塵埃が限定された清浄度レベル以下に管理されたクリーンルームが必須となります。クリーンルームについては、下記の記事で詳しく解説しています。
金属汚染
蒸発した汗に含まれるナトリウム分子や、薬液に含まれる微量な重金属原子などがあります。
これらの表面汚染は、濃度が微量でもデバイスの電気特性を大きく劣化させ、余分な電気を流してしまうことがあります。
有機汚染
人のフケや垢に含まれる炭素、工場内で使う薬液に含まれる微量の炭素分子などがあります。
油脂
人の汗に含まれる油分や製造設備で使用するグリスなどがあります。
ウェーハの洗浄方法は物理的に除去するか、化学的に除去するかに分けることができます。
- 物理的(メカニカル)除去
①ブラシなどによる機械的なもの
②超音波による振動
③氷粒子エアゾルの吹付けなど - 化学的(ケミカル)除去
①溶解反応
②リフトオフ除去
これらはいずれも薬液などを用いるウェット洗浄です。現在使われている洗浄のほぼ99%はウェット洗浄ですが、酸素ガスやオゾンガスで洗浄を行うドライ洗浄というものもあります。
次に洗浄の基本であるRCA洗浄について説明します。
RCA洗浄
RCA洗浄とは、シリコンウェーハの標準的な洗浄方法です。
RCA社のWerner Kernが1965年に基本的なプロセスを開発したものであり、化学的な作用による洗浄方法の代表で、薬液の組み合わせによる洗浄液を用いる方法です。
アンモニア水と過酸化水素水の混合溶液(Standard Clean1: SC1と呼ばれる)処理により、ウェハ表面に付着している有機物の除去を行い、純水リンスを行った後に塩酸水と過酸化水素水の混合溶液(Standard Clean 2: SC2と呼ばれる)処理で金属不純物を溶解、除去し、純水リンスを行い、最後に乾燥を行います。
洗浄装置として最も普及しているのはウェットステーションです。ウェットステーションとは薬液の入った槽や純水の入った槽が並んだ装置で、これらの槽の中に多数のウェーハ(通常は50 枚)をまとめて浸して、汚染物を溶かしたり、中和したり、洗い流したりした後に乾燥させます。
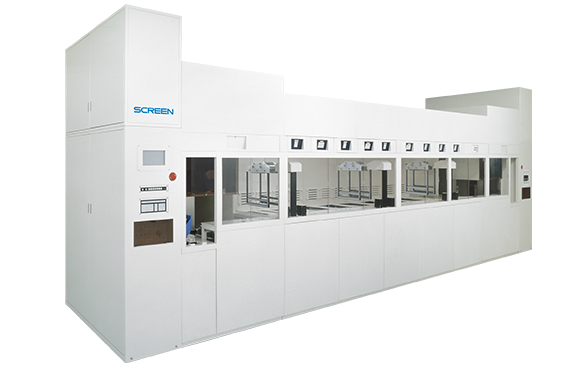
バッチ式
バッチ式とは、ウェーハを複数枚まとめて処理する方式です。バッチ式の洗浄装置は、上記のウェットステーションです。
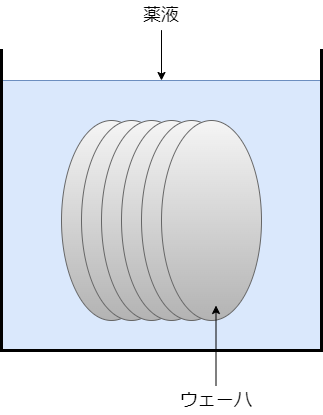
たくさんのウェーハが一括で処理できるということはそれだけコストダウンにつながります。洗浄プロセスのように回数の多いプロセスには有利です。
薬液の種類ごとに処理槽を用意し順番に浸漬する「多槽ディップ式」と、一つの槽で薬液を入れ替えながら洗浄する「単槽式」に分類されます。
枚葉式
枚葉式とは、ウェーハを1枚1枚処理していく方式です。
枚葉式は、洗浄面を上にしたウェーハを水平方向に回転さて、そこにノズルから薬液を吹き付けて洗浄します。
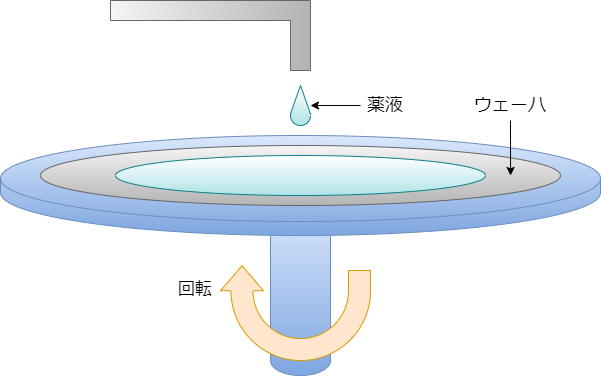
メリットは、バッチ式と比較して装置の構造がシンプルで小型化ができるので、装置のコストを下げることができます。また、1枚ずつ処理条件を変更することができるので、多品種少量生産に向いています。
一方、デメリットとしては装置の配管が複雑になりメンテナンス性が悪くなったり、バッチ式と比較して1枚あたりの処理時間が長くなってしまします。
近年はプロセスの微細化に伴い、より精密に洗浄できる枚葉式が主流になってきています。
ウェーハは、洗浄したらすぐに乾燥しないと表面が酸化したり、ウォーターマークと呼ばれる汚染が発生します。
ウォーターマークとは、ウェーハが濡れた状態から乾いた状態に移る過程で、ウェーハ表面に水分が残留することにより生じるシミのことです。ウォーターマークは、パーティクルと同じようにデバイスの欠陥を引き起こします。
洗浄プロセスは、ウェーハを乾燥状態で出し入れするドライイン・ドライアウトが原則です。
- スピン乾燥
ウェーハを高速回転させて水分除去する方法です。装置の構造が簡単で、効率よく乾燥させることができるが、回転によって塵や静電気が発生するのが課題です。 - IPA乾燥
水分をIPA(イソプロピルアルコール)蒸気で置換します。塵や静電気の問題を避けることができる一方、引火性があるため事故の危険も伴います。 - マランゴニ乾燥
ウェーハを純粋層から引き上げる際に、水面にIPAを添加し、表面張力(マランゴニ効果)の働きを利用して水分を除去します。IPAのみの乾燥に比べて、IPAの使用量が少なくすることができ、主にバッチ式で用いられます。
- SCREENホールディングス(日本)
- 東京エレクトロン(日本)
- Lam Research(米国)
SCREENホールディングスは、「枚葉式洗浄装置」「バッチ式洗浄装置」「スピンスクラバー」という3種類の洗浄装置で世界シェア1位です。
洗浄プロセスは、半導体デバイスの歩留まりや品質に直接影響を及ぼします。不純物や汚染物質がウェーハ上に残ると、トランジスタやその他の電子デバイスの性能が低下する原因となります。正確で効果的な洗浄プロセスによって、デバイスの信頼性が高まり、製造コストの削減にもつながります。
- エレクトロニクス市場研究会「図解即戦力 半導体業界の製造工程とビジネスがこれ1 冊でしっかりわかる教科書」、技術評論社 (2022/3/2)
- 佐藤淳一「図解入門 よくわかる半導体プロセスの基本と仕組み」、秀和システム (2020/8/29)
- SCREENセミコンダクターソリューションズ